Are Sustainable Homes and Modular Construction on a Collision Course
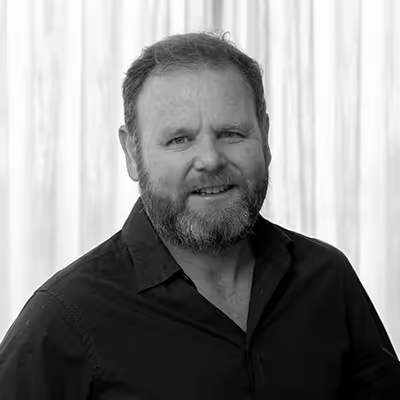
Written By
Craig Sutton
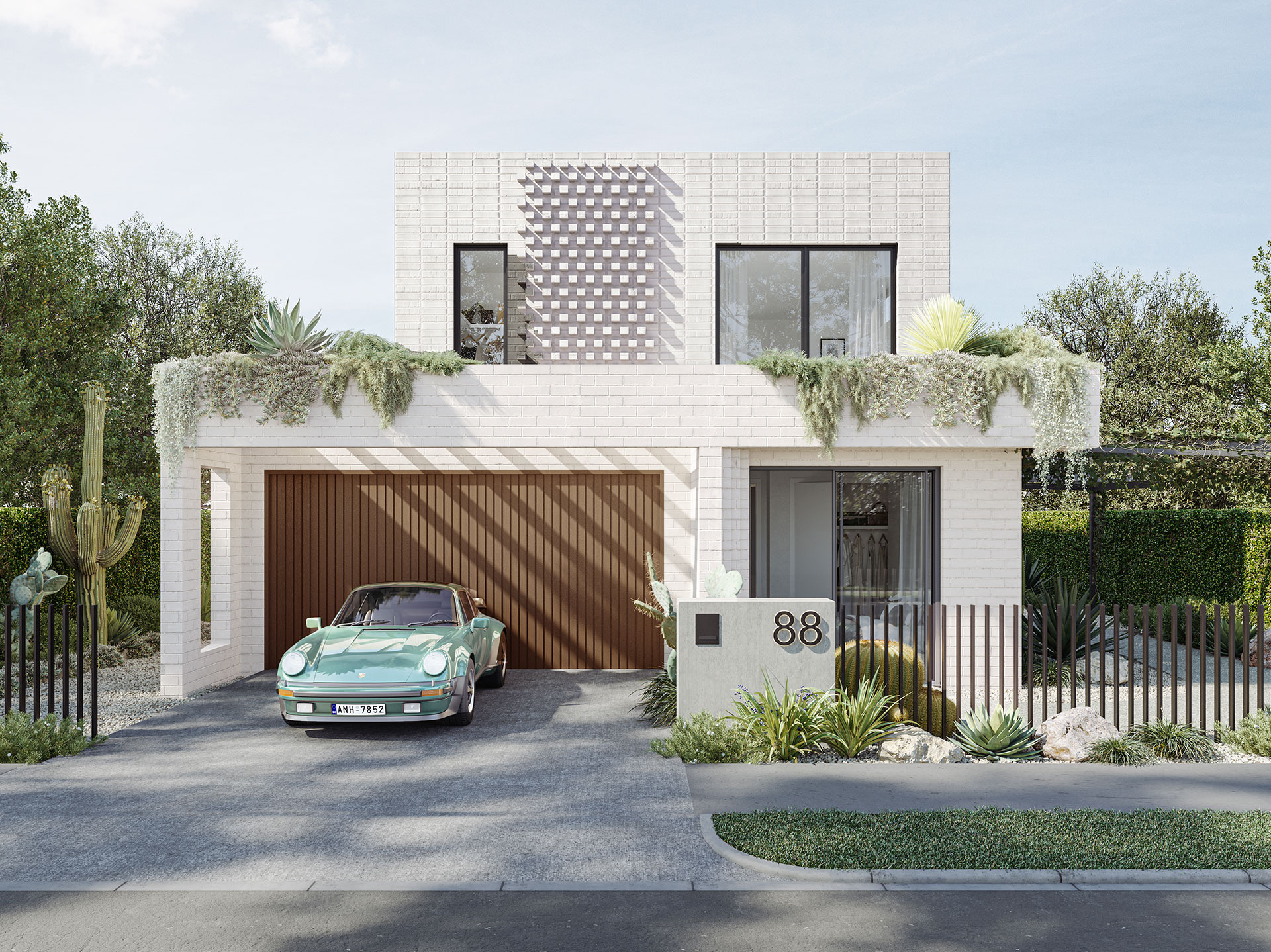
In the evolving landscape of Australian residential construction, we’re facing a complex and consequential tension—one that underscores the nation’s broader struggle to build smarter, faster, and more sustainably.
On one side: increasingly stringent environmental standards, like NatHERS and BASIX, which demand site-specific, performance-optimised homes. On the other: the rising promise of modular and prefabricated construction, heralded as a scalable, cost-effective solution to our housing supply crisis.
Individually, these shifts represent positive progress. But together, they introduce a powerful friction point—because what enables one, often undermines the other.
And it’s in this tension that the future of homebuilding in Australia must now be reimagined.
Theme One: Sustainability Demands Context—And Customisation
Environmental legislation is no longer a side note in the design process. It's the headline.
Frameworks like NatHERS and BASIX increasingly require homes to be fine-tuned to their specific site—to the sun, wind, slope, and thermal properties of the environment in which they’re built. It’s not just about efficient appliances or rooftop solar anymore. It’s about passive design, insulation performance, window placement, and how all of these interact with a home’s orientation and location.
But that’s only the beginning.
In urban infill and brownfield development—where a significant portion of future housing growth is set to occur—the complexity amplifies. Sites are increasingly constrained by different council regulations, existing trees, stormwater management, flood overlays, asset protection zones, privacy and overshadowing controls, and legacy easements and infrastructure. These aren’t minor hurdles; they are major design-shaping forces that demand bespoke responses.
In this environment, customisation isn’t a luxury—it’s a necessity.
Theme Two: Modular Efficiency—Built for Speed, Struggling with Variation
Meanwhile, modular and prefabricated construction has captured the imagination of governments and developers alike. And rightly so. The benefits—faster build times, reduced waste, fewer weather delays, and potential cost savings—are compelling in the face of acute housing undersupply.
But these systems were designed for a different kind of challenge.
Modular construction thrives on high levels of standardisation. The business model only works when production is predictable, repeatable, and efficient. Large automated factories rely on economies of scale, and require high utilisation rates to justify their significant capital investment.
Unlike traditional construction firms, which can scale labour up or down with project cycles, factories carry fixed costs that are far less flexible. When demand dips—whether due to interest rates, planning delays, or broader market cycles—factories can't simply “shed a few tradies.” Their equipment, maintenance, floor space, and technical staff remain costly, regardless of how many homes are in the queue.
And herein lies the conflict: to meet environmental and site constraints, we need homes to be more adaptive. But to make modular cost-effective, we need homes to be more standardised.
Theme Three: A Systems Challenge—Not Just a Design One
This isn’t simply about form versus function. It’s about the systems we build around construction—financial, regulatory, technological—and whether they can accommodate both customisation and scalability.
The solution won’t be found in choosing one path over the other. It must be found in innovative convergence.
We must explore models where modular systems are built for modularity of response, not just of component. Where adaptive templates allow for site-specific tweaks without derailing production efficiency. Where digital engineering tools, BIM, and generative design software can streamline compliance with trees, flood zones, and solar access without reverting to full custom builds.
Equally, we must invest in new economic models for prefabrication—ones that de-risk capital-heavy operations through multi-sector partnerships, public pipeline guarantees, or flexible production models that extend beyond just residential.
Design for Complexity, Build for Adaptability
Australia’s construction future will not be solved by a single method or ideology. We must acknowledge the messy, dynamic, and highly localised realities of building today, particularly in urban environments where every site tells a different story.
We need homes that are designed for complexity, but built with efficiency. We need policy settings that reward adaptability, not just compliance. And we need industry leaders willing to invest in innovation that bridges this growing divide.
The challenge is great—but so is the opportunity. Let’s not settle for homes that are just faster or greener or cheaper. Let’s aim for homes that are smarter, more liveable, and more reflective of the land and lives they’re built to serve.
1
min read
March 4, 2025
Resources
Design Guides
Journal
More News Articles
Let's Start a Conversation
Quick Links
Resources
Contact
Subscribe to our newsletter
Copyright 2024 Builders Licence 275897c Privacy Policy. Powered by TAG